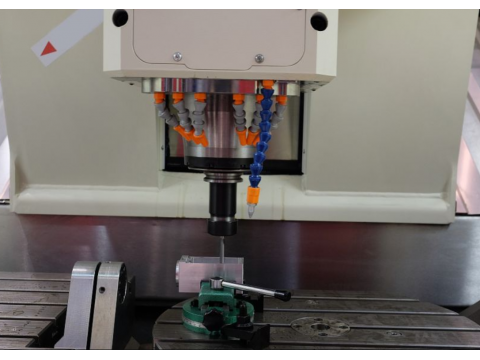
粤港澳大湾区(广州)超级充电桩展览会
2024-08-24~2024-08-26
广交会展馆D区
中国(成都)绿色能源发展大会 第二十一届四川国际电力产业博览会
2024-05-23~2024-05-25
成都世纪城新国际会展中心
IOTE 2024上海beplay体育注册登录 展邀请函
2024-04-24~2024-04-26
上海世博展览馆
2024 第 19 届中国(重庆)橡塑工业展览会
2024-05-23~2024-05-25
重庆南坪国际会展中心
数智工厂?智慧物流 2024中国(广州)国际物流装备与技术展览会
2024-05-29~2024-05-31
中国进出口商品交易会展馆D区
2024中国国际锂电池技术装备展
2024-04-12~2024-04-14
宁波国际会展中心(鄞州区会展路181号)